Comprehending Porosity in Welding: Discovering Causes, Results, and Avoidance Strategies
Porosity in welding is a relentless challenge that can considerably impact the high quality and stability of welds. As professionals in the welding market are aware, understanding the causes, impacts, and prevention methods connected to porosity is critical for attaining robust and reliable welds. By diving right into the origin of porosity, analyzing its detrimental effects on weld top quality, and exploring reliable avoidance approaches, welders can enhance their knowledge and abilities to produce top notch welds regularly. The intricate interaction of variables contributing to porosity needs a comprehensive understanding and a positive approach to make certain effective welding end results.
Usual Sources Of Porosity
Contamination, in the type of dust, grease, or rust on the welding surface area, creates gas pockets when heated up, leading to porosity in the weld. Improper shielding takes place when the securing gas, generally made use of in procedures like MIG and TIG welding, is not able to totally secure the molten weld swimming pool from responding with the surrounding air, resulting in gas entrapment and succeeding porosity. Additionally, inadequate gas insurance coverage, typically due to inaccurate circulation rates or nozzle positioning, can leave components of the weld unguarded, enabling porosity to develop.
Effects on Weld Top Quality
The visibility of porosity in a weld can substantially compromise the general quality and honesty of the welded joint. Porosity within a weld develops voids or cavities that damage the structure, making it much more vulnerable to fracturing, rust, and mechanical failure. These voids work as tension concentrators, decreasing the load-bearing ability of the weld and raising the possibility of early failure under applied stress. In enhancement, porosity can also work as prospective websites for hydrogen entrapment, further exacerbating the degradation of the weld's mechanical homes.
Furthermore, porosity can prevent the efficiency of non-destructive screening (NDT) methods, making it testing to spot various other issues or gaps within the weld. This can result in substantial safety and security issues, particularly in crucial applications where the structural honesty of the bonded elements is vital.
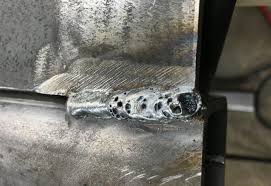
Prevention Techniques Review
Offered the detrimental effect of porosity on weld quality, effective avoidance techniques are crucial to preserving the structural honesty of welded joints. Additionally, find this picking the ideal welding specifications, such as voltage, current, and take a trip rate, can aid decrease the danger of porosity formation. By including these avoidance methods right into welding methods, the occurrence of porosity can be considerably minimized, leading to stronger and a lot more dependable bonded joints.
Significance of Appropriate Shielding
Proper protecting in welding plays a crucial role in stopping atmospheric contamination and guaranteeing the stability of welded joints. Shielding gases, such as argon, helium, or a mix of both, are generally utilized to secure the weld pool from reacting with elements airborne like oxygen and nitrogen. When these reactive aspects enter into call with the hot weld pool, they can trigger porosity, causing weak welds with minimized mechanical homes.
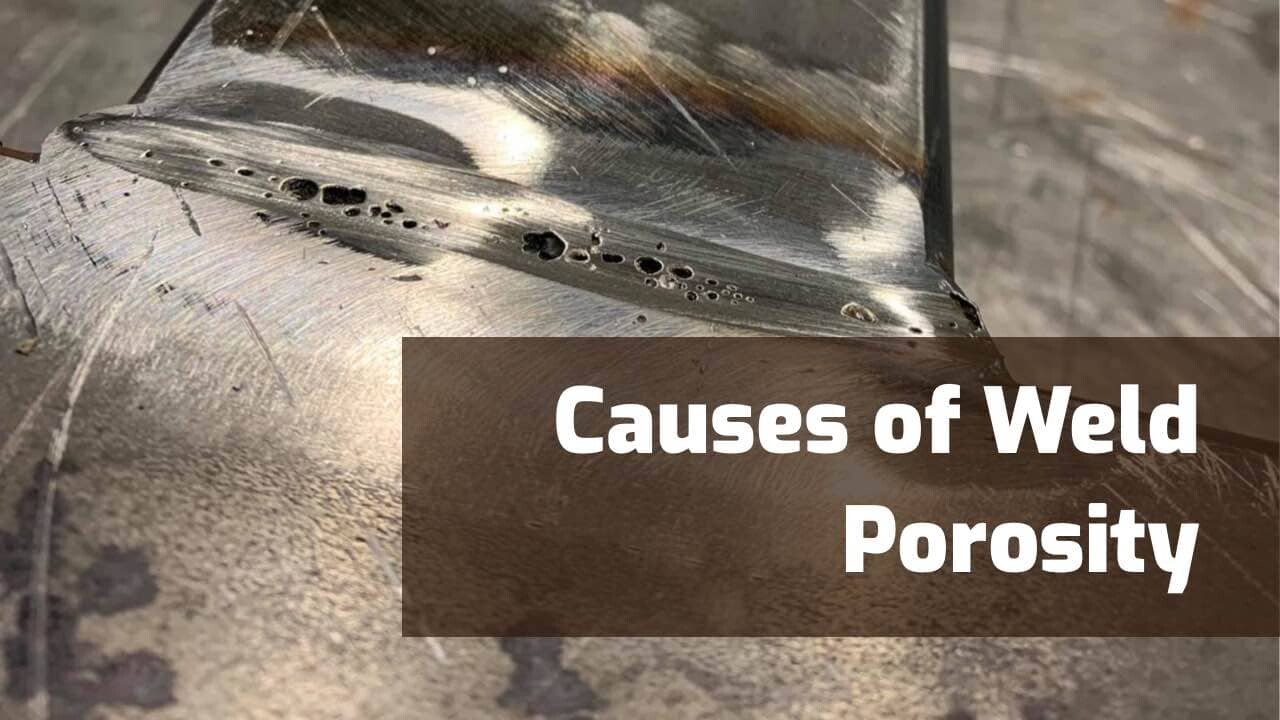
Poor protecting can cause different flaws like porosity, spatter, and oxidation, jeopardizing the structural honesty of the welded joint. Adhering to appropriate shielding methods is crucial to create high-grade welds with minimal defects and ensure the durability and reliability of the welded elements.
Tracking and Control Methods
How can welders effectively keep an eye on and regulate the welding procedure to make sure optimum results and protect against issues like porosity? One key method is through using innovative tracking technologies. These can consist of real-time tracking systems that offer comments on specifications such as voltage, existing, take a trip speed, and gas flow rates. By continually keeping an eye on these variables, welders can determine inconsistencies from the perfect conditions and make prompt adjustments to stop porosity formation.

Additionally, carrying out correct training programs for welders is important for monitoring and controlling the welding procedure successfully. What is Porosity. Enlightening welders on the relevance of preserving consistent criteria, such as correct gas shielding and take a trip rate, can aid prevent porosity issues. Routine assessments and qualifications can additionally ensure that welders are competent in monitoring and managing welding procedures
In addition, the use of automated welding systems can enhance monitoring and control abilities. These systems can precisely regulate welding parameters, decreasing the chance of human mistake and guaranteeing regular weld top quality. By Click Here integrating advanced tracking modern technologies, training programs, and automated systems, welders can successfully monitor and regulate the welding procedure to decrease porosity problems and accomplish top notch welds.
Final Thought
